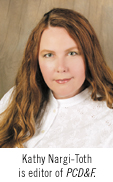
All that glitters is certainly not gold, and the glitz of Las Vegas added no shine to the recent trade event, IPC APEX EXPO held there. Official numbers put attendance down 34.5% YoY.
There were however, some takeaways from the conference and forums that ran concurrent to the exhibits. In the IPC Government Relations committee meeting, Nilesh Naik, CEO of One Source Group, contributed interesting information on the R&D tax credit that is back on the books retroactively for 2008 and in effect through the end of 2009.
According to the discussion, scrap generated when developing or modifying a process can be considered an R&D activity. For tax purposes, R&D is not limited to laboratory experiments. The list of qualified R&D activities includes the development of new or improved products, manufacturing processes, production equipment, software used in a production process or the design of fabrication tools and dies. Generating prototypes and first articles of new products for testing and validation qualifies. Conducting tests to satisfy foreign regulatory requirements (RoHS anyone?) will qualify. Even evolutionary (versus wholesale) changes in operations and production lines are eligible. Manufacturing companies account for the majority of businesses claiming the credit, but one estimate given by Manufacturing.net indicated that over 40% do not take advantage of the potential savings on bona fide development investment.
It’s a good way to lower a company’s annual net cost of technology improvements. According to Naik, R&D tax credits will save One Source Group almost $100,000. A general note of caution: This is a specialized area of tax law that may require the services of a larger CPA firm with more diverse experience. It also behooves the manufacturer to maintain good recordkeeping to capture the qualified R&D expenses from year-to-year because it is the annual increase in investment that is captured in the tax credit. Manufacturing.net has an excellent overview article (“How to Realize the Benefits of the R&D Tax Credit”) that outlines the process and accounting procedures.
Speaking of R&D, there were a number of notable new technologies shown at IPC APEX EXPO, many of which will be covered in more detail in PCD&F over the next few months, through a combination of technical papers and company interviews. One technology in particular caught my attention, a process for generating RFID tags in a roll-to-roll format.
This novel idea is the brainchild of Conductive Inkjet Technology (CIT), a subsidiary of Carclo, a large, publicly held firm that makes injection molded plastic components for automotive, telecom, medical and optical applications.
The process is simple. The catalytic ink is digitally printed via inkjet onto a plastic substrate, like polyester. Then, the ink is UV and IR cured. After curing, it is immersed in an electroless copper solution, then rinsed and dried. It is a fully additive process that inherently generates less waste than a subtractive, print-and-etch method. The target thickness for the catalytic ink is 6 microns and the copper thickness is 1 micron to 2 microns.
The copper thickness will not be sufficient for every application and, according to CTI, is not applicable for low frequency (100 to 500 kHz) applications. It may be workable in some high frequency (10 to 15 MHz) applications. It definitely has niche with UHF (650 to 950 MHz) and microwave (2.4 GHz to 5.8 GHz) products. In the UHF and microwave range, thin copper actually performs better than thicker silver conductive inks, and at a lower cost.
One of the equipment partners is well-known in fab circles. Cemco FSL is building the electroless copper roll-to-roll plater. The continuous inkjet equipment is specifically designed for this application, using a print engine from Inca Digital Printers with Spectra SE-128 heads in a standard Inca print bar. These have been integrated with a high-end web transport from Alpha Converters.
In ROI this month (pg. 11), Peter Bigelow covers a few additional technologies for consideration by PCB fab and assembly companies looking to diversify their portfolios and capitalize on their in-house knowledge base and talent pool. RFID tags may offer another opportunity. According to CTI, an investment in the range of $1 million is all that is needed to get started. Money invested in R&D this year, or funneled into an alternative manufacturing startup, might just turn into next year’s silver lining.