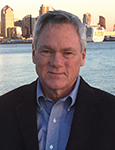
Know what drives cost – and what doesn't.
We get this question a lot: “How much per square inch for a four-layer board (or double-sided, or six layers)? I won’t hold you to it, I promise.” Right….
We get it. It’s difficult to provide the boss with a project cost rollup without the board cost estimate. If you do a lot of designs, you may have a feel for it, or you may refer to a similar board cost from a past project. This actually can be very effective.
I have even seen online cost calculators that presume to give an accurate number. Knowing what I know about PCB pricing, however, I can say it just ain’t so.
Here is why calculating PCB cost is tricky and dangerous ground.
The biggest cost drivers for a bare board are:
- Who are you? Are you a stranger or newcomer, or do you have established relationships with board vendors? Most of us manufacturers figure the total dollar volume somewhere into the pricing equation.
- Board size. Square area of the board, plus the square inches of material remaining on the panel after routing your unique board shape. (You are charged by the processed panel.)
- Production volumes in the 10 boards to 1,000 boards range will have a very steep cost curve. The curve flattens out as the order rises above 1,000 and gets very unpredictable at 100,000. Who you are begins to make a big difference at this level, along with your negotiating skills.
All manufacturers have a floor or minimum, and it is best to ask how many boards you can get for the minimum charge. Some of the internet guys will sell one or five at a seemingly low cost, but your boards will have to fit perfectly into their narrow technical profile.
- Delivery requirement. In the one-to-10-day requirement range there can be a very steep cost curve. After 10 days, this has little influence, unless the volumes are large. Boards can be turned from China to the US in as few as five days, albeit with certain expediting fees.
- Manufactured location. USA, China, Europe, Taiwan. This is usually a preferential decision, but clearly China has the edge, followed by Taiwan. Differences can be great.
- Number of layers. No surprise here. From double-sided to four layers, costs will go up about 60%. From four layers to six add another 50%. For six to eight layers add 30%. Keep in mind each added layer is the equivalent of a double-sided board added to the stack. Also, remember high-layer-count boards are often accompanied by tough technical requirements and buried vias.
- Technology stretching requirements, like exotic materials, super small geometries, buried vias, etc. This can be steep or moderate, depending on the manufacturer and the difficulty. Tg requirements will have a moderate impact.
- Surface finish choice, such as HASL, ENIG, tin, OSP. If you can handle OSP, it is the lowest cost, followed by HASL, then ENIG. ENIG is so common these days that for low volumes it can be as low cost as HASL.
But not the following:
- Number of drill hits; however, the total number of drill tools used can drive up costs. Ten tools is the preferred maximum and usually can do the job.
- Presence or absence of a silk screen legend. (Minor influence.)
- Testing: Always insist on no charge.
So, now think about putting all of this into an algorithm and coming up with a defensible, unchangeable answer. That is a dangerous guessing game.
My best advice is this: Get preliminary Gerbers to your preferred vendors and tell them they are preliminary. If the effort is conceptual, provide a simple description answering the cost drivers above and email your proposed or preferred vendors for a quote. In some cases, suppliers will make this easier by offering a template.
Thomas Smiley is founder and president of Precision Circuit Board Source (precisionpcbs.com).