Computational fluid dynamics-based simulations that examine
temperature and heat flux can help engineers make better thermal
management decisions.
Simulation methods that provide predictions
of thermal behavior for an electronics system are many and varied. One
characteristic shared by these methods is the prediction of
temperatures at many locations between heat sources and the cool
ambient temperature. Relating the component temperatures (i.e. heat
sources) to their maximum-rated temperature will determine thermal
compliance.
This observational approach to simulation is valid
but, by further examining other outputs, an understanding of why the
temperatures are what they are is possible. With this additional
knowledge, more-informed design decisions can be made to resolve
potential thermal design flaws.
Computational fluid dynamics (CFD)
is a software-based simulation technology that enables the prediction
of various physical properties at literally hundreds of thousands of
discrete locations in and around an electronics system. Pressure,
velocity and temperature values are predicted in the air, while
temperature and heat fluxes are determined within solid materials. Such
a wealth of data would be impossible to obtain experimentally. The
following two examples highlight how, by examining not only
temperatures but also heat flow paths, one specifically can learn why a
thermal design is underperforming or over designed.
Thermal Vias Carry Heat Down and Out
The
first example evaluates a ruggedized design in which a printed circuit
board (PCB) is wedgelocked inside a sealed enclosure, providing a
conduction-cooled thermal environment. A good thermal design would have
the heat leaving the components, conducting down to the internal
copper-molybdenum-copper stiffening layer in the PCB and out through
the wedgelock to the heatsinking fins on the outside of the enclosure.
A 44-pin small outline integrated circuit (SOIC) package is powered at
2.0 watts, making it the most thermally critical on the board.
The temperature results of an initial CFD simulation are shown in
FIGURE 1.
The temperature plot indicates a junction temperature of 142.8° C, with
the temperature reducing as the heat spreads throughout the package. It
is the equivalent heat flux plot shown in
FIGURE 2, however, that provides the greatest insight. Heat flux is defined in terms of W/in
2
and can be considered somewhat analogous to current density. It clearly
shows the dominant paths the heat follows as it leaves the package,
unlike the temperature plot where such distinctions are not observed.
Heat is seen to leave the die, through the leadframe and along the top
signal layers. Some heat does conduct down to the internal-stiffening
layer as intended, but the intermediate, thermally resistive dielectric
layers create a pronounced thermal break.
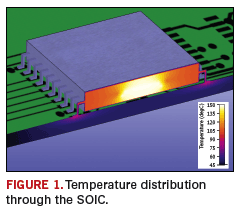
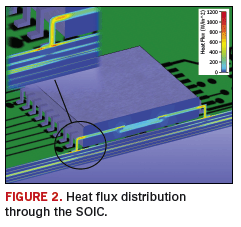
There
are several ways to remedy such a heat flow path discontinuity. The
first is to add thermal vias directly under the pads, linking the
present heat flow path directly to the innerlayers. This would be
difficult to achieve from a routing perspective. An alternative is to
attempt to link the die directly with the internal layers. This is
achieved in two stages. First, change the package style to an exposed
pad SOIC, which is soldered onto a matching land on the PCB. Secondly,
include an array of thermal vias under the land that connects down to
the stiffening layer.
FIGURE 3 shows the resulting heat flux
plot for this configuration. In this example, the junction temperature
rise decreases by 41.4%, down to 88.6° C, now below the maximum rated
junction temperature of 100°C.
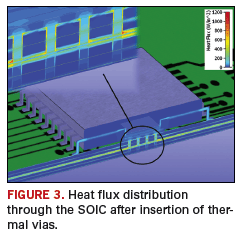
It is commonly
accepted that for natural convection-cooled (no fans moving the air)
and conduction-cooled environments, adding more copper to the board
will help the thermal performance. Following this advice and applying
it to the previous example might have led to a decision to simply
increase the thickness of the stiffening layer. By understanding the
concept of a continuous, dominant heat flow path to the cooling
ambient, one can appreciate the more effective approach of using
thermal vias and an exposed pad. In fact, once a continuous heat flow
path has been designed in, one can start to further reduce the overall
resistance by adding as much copper as possible along that path,
including the internal layers.
Before moving on, it’s worthwhile
to elaborate on the differences between electrical and thermal
resistivities. The difference between the electrical resistivity of
copper and FR-4 is approximately 20 orders of magnitude. The equivalent
difference between the thermal resistivity (taken to be the inverse of
the thermal conductivity) is only 3 orders of magnitude. It is because
of these ratios that the electrical current travels exclusively within
copper, while the heat tends to follow the copper and to spread through
the FR-4. The apparent breaks in the heat flow paths in Figure 1 do not
mean that heat is unable to leave the system to the ambient. Instead,
it is forced to spread and to pass through the more thermally resistive
FR-4 regions on its way out. This causes an increase (build up) of
temperature back down the heat flow path and ultimately to the source.
CFD Analysis Helps a Heat Sink Lose Weight
The
second example contains probably the most common of all electronics
cooling solutions: a heat sink. The name is somewhat misleading in that
a heat sink does not provide a pit into which the heat is magically
absorbed, thereby removing it from the system. The heat sink does,
however, play a critical role in connecting the heat sources with the
cooling ambient air by decreasing the thermal resistance from the
package surface to the ambient air. Conductive thermal resistance is
formally defined as:

where R is the thermal
resistance (K/W), δ is the material length through which the heat
passes (m), k is the thermal conductivity of the material (W/mK) and A
is the area through which the heat passes (m
2).
Compared
to a bare component surface, the heat sink results in a decrease in R
due to the fact that it provides a much larger cooling area, (A). This
“area extension” far outweighs the fact that the heat has to pass a
certain distance (δ) through a material with thermal conductivity (k).
For
a given volume, a heat sink takes heat from a point source (or a series
of point sources) and spreads it to a large surface area, where air
then convects it away. Heat sinks have two main parts, a base and a
series of fins. The base spreads the heat sideways to the base of each
fin. The heat then conducts up only the fins having a large surface
area in relation to their volume (they are long and thin).
One
might think that having as many thin fins as possible along the base
would be the most optimal design; however, the smaller the air gap
between the fins becomes, the less likely it is that air will be able
to squeeze through to convect the heat away. Ultimately, this traps
stagnant air that, unlike moving air, is very thermally resistive.
Alternatively, using too few fins decreases the surface area and
detracts from the beneficial effect of the heat sink.
A good
heat sink thermal design is a trade-off between thermal effectiveness,
weight and cost. This is the basis of the second example. A power
supply unit has a single fan blowing air through a large heat sink that
has 10 TO-220 power invertors. These invertors dissipate 9.5 W each and
are connected to the heat sink base. Each inverter has a maximum-rated
junction temperature of 100° C, and one of the design goals is to
minimize the total mass of the unit.
An initial CFD thermal
simulation of the system indicates that each inverter is thermally
compliant, with a maximum junction temperature of 93.3° C. By examining
the heat flux distribution within the heat sink, it is possible to
identify, and perhaps eliminate, parts of the heat sink that are not
contributing to heat removal.
FIGURE 4 shows the distribution of heat flux on a plane at the mid-height of the fins, and
FIGURE 5
shows this through the middle of the heat sink. The heat flux colors
are clipped above a maximum and below a minimum value for clarity. The
periphery of the heat sink, including the upstream and downstream ends
of the fins and the far left and far rights fins, does not receive much
heat because of low heat flux values in those areas.
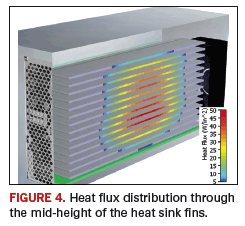
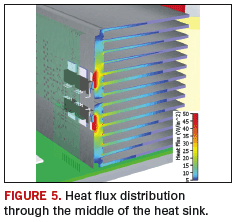
In
theory, these sections of the heat sink could be removed without unduly
compromising thermal performance. This is investigated in a second
study in which the heat sink length and fin height are reduced by 10%,
and the two outermost fins are removed altogether. The maximum junction
temperature increases slightly to 94.4° C, but more importantly, the
total heat sink mass is reduced by nearly 30%.
Conclusion
Whereas
generalities such as “more copper in a PCB makes things cooler” and
“the bigger the heat sink, the better” are often valid, a greater
understanding of heat loss paths through a series of thermal
resistances enables more refined conclusions. Thermal design decisions
and remedial actions can be applied effectively and implemented with
little risk of failure.
The necessary understanding can be
gained by examining both the temperature and the heat flux results of a
CFD-based simulation. Whereas temperature alone enables an
observational method of determining thermal compliance (is it too
hot?), heat flux simulation explains why the temperature is what it is.
PCD&FRobin Bornoff is the FloTHERM and FloVENT product marketing manager for Mentor Graphics Corporation.