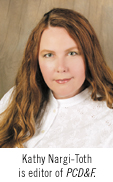
You know the adage: A picture is worth a thousand words. In medical electronics, pictures often make the difference between a fast, accurate diagnosis and a prolonged illness. A few months ago, two computer engineers at Washington University in St. Louis added millions of words to the picture of healthcare that rural communities will have access to. William D. Richard, Ph.D., and David Zar coupled a redesigned ultrasound probe with a smartphone to create a completely mobile, infinitely transportable, ultrasound unit. The ramifications are far-reaching, especially for a majority of the world’s population, which lacks access to medical imaging but does have cell phone service. This type of tool is also seen as a way to move some of the rudimentary tasks of data gathering out of the hospital and into the hands of trained laypeople and caregivers, thus reducing healthcare costs.
Medical electronics is one of the fastest-growing segments, and one that is particularly resistant to economic influences. People get sick in times of plenty or in times of want. According to Databeans, in 2008, medical electronics accounted for about 7% of the industrial semiconductor market and is expected to grow by 67% over the next five years.
Many of these new devices will use flexible circuit boards to facilitate wearable configurations that provide monitoring and support for patients with chronic conditions. In these applications, high-density packages, miniaturization and low power consumption, coupled with powerful signal processing and compact communication capabilities are key. In the design of these diagnostic tools, semiconductor and interconnect platform engineers are being challenged to reshape the definition of miniature because in no other application is there such a constraint on size.
Wearable and implantable medical devices are reshaping the face of the medical electronics marketplace. These types of products are consumer-driven, like cell phones and PCs, and design considerations must conform to whims and wallets. Clunky devices are being replaced by trim, stylish tools more akin to an iPod than to monitoring or diagnostic instruments found in hospitals.
Adding the consumer to the medical electronics prescription is like liposuction in the time-to-market equation, putting electronic designers under the microscope to come up with smaller, faster products in months, instead of the traditionally longer cycles associated with these products. The designs need to pay close attention to the potential for parts obsolescence because FDA approvals for completed systems can take as long as 36 months.
With the migration of medical diagnostic and monitoring systems from hospital to home, there comes another fundamental change in system design as it focuses on user ease, safety and reliability. The bar for safety and reliability has always been high in this segment, but once the tool is taken from the hands of the trained medical professional and placed in the hands of the consumer, it takes on another dimension. There will be no back-up unit or experience-hardened professional in the home to fix a problem.
All of this puts the electronics designers in a particularly perilous position. The components most likely to meet the form factor and performance requirements needed for today’s wearable and implantable devices can be readily found in the consumer electronics market. Unfortunately, these state-of-the-art parts are the very ones with the shortest product lifecycle and quick obsolescence, and therefore, are not well-suited for the protracted qualification cycles associated with medical products.
The brave new world of wearable, implantable and transportable medical electronics will offer designers and fabricators a host of new opportunities. The current market model for medical gear places manufacturing close to point of use, and the aging US population can certainly provide legions of users. This may change as pricing pressures drive this emerging volume market into lower-cost manufacturing centers, as we saw with cell phones and other consumer products. And if manufacturers in the US come up short on the technology curve again, this potentially lucrative niche may find a ready-made home in the rapidly advancing HDI factories in China and elsewhere around the world.